Case Study: Surface Treatment with Water Jet: Rail Cleaning
Introduction and project overview
The fall of autumn leaves results in their direct deposition on the railhead or their redistribution by vehicle-induced airflow. This organic material reacts and bonds to the railhead, forming a black layer that causes ultra-low friction conditions. A novel abrasive/water jetting railhead cleaning system has been designed to address this issue. The system underwent trials aboard a Class 153 vehicle at East Lancashire Railway over four days. A representative organic layer was simulated by applying powdered leaf material on the railhead and rolling it with a vehicle until it blackened and bonded to the underlying steel. The cleaning performance was quantified using a Rivelin Rail portable railhead tribometer, railhead imaging, and layer thickness data.
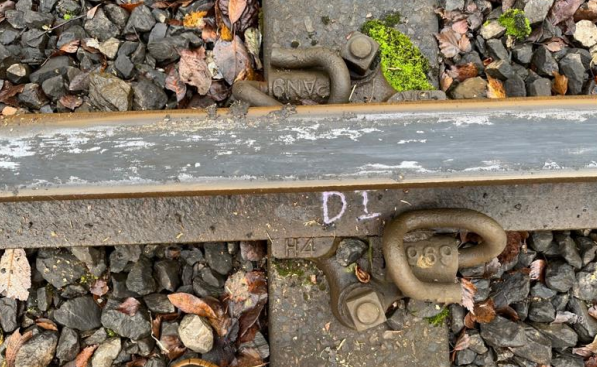
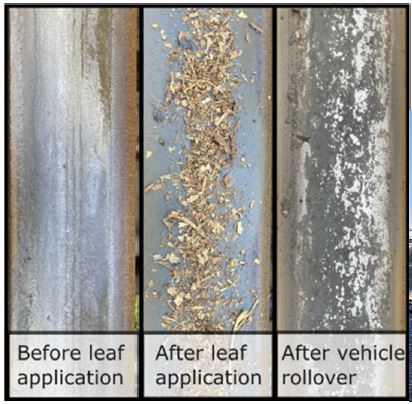
Project description
Railhead Conditioning
Railhead conditioning was performed to create a representative level of leaf contamination, simulating low-friction conditions requiring cleaning during the autumn season. Blended fresh Sycamore leaves were placed on the railhead after light sanding to expose bare steel, followed by rolling with a Pacer vehicle to blacken and bond the leaf layer to the steel.
Railhead Measurements
The Rivelin Rail portable railhead tribometer measured railhead friction by clamping magnetically to the railhead and using a rotating steel wheel (this wheel replicates similar pressures to that of an actual train wheel/ rail contact, 700 Mpa). Friction measurements were taken before and after each cleaning run. Eddy current layer thickness measurements were also taken to assess the effectiveness of cleaning.
Railhead Cleaning
A Class 153 equipped with the novel railhead cleaning system was used for cleaning runs at designated speeds. The cleaning system operated at 750 bar, using abrasive particles and water.
Summary
The typical test run method included sanding the rail surface, measuring wet baseline friction coefficient, applying leaf powder, rolling over with a Pacer, cleaning with the Class 153, and measuring friction coefficients after each cleaning pass.
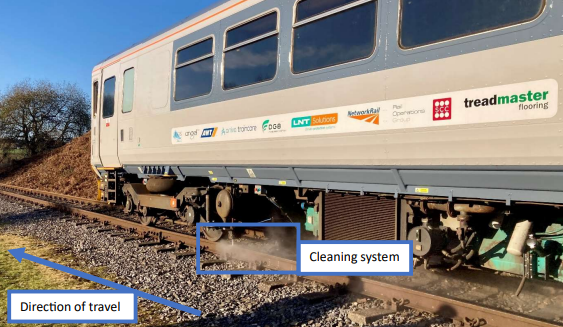
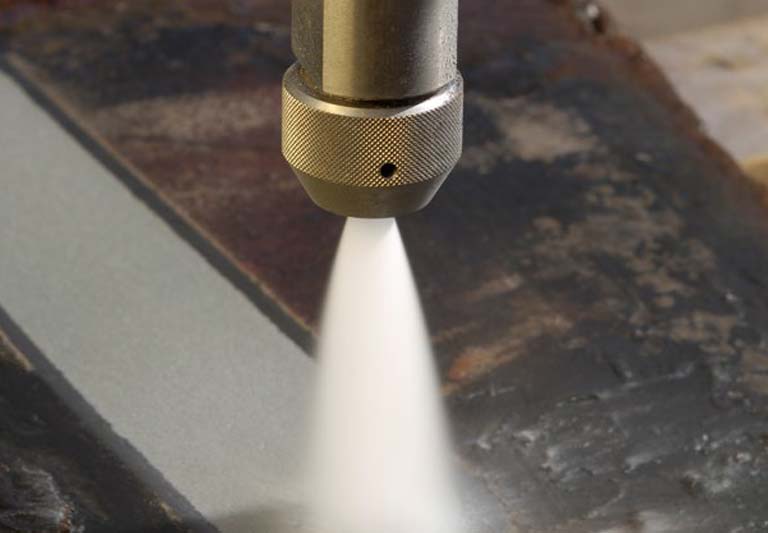
Results
Friction measurements showed a statistically significant increase after the first cleaning pass, with mean average coefficients above 0.09 on all test days, which is considered to be the minimum value required for braking under typical operating conditions according to the GB schedule. This increase in friction validates the efficacy that, the novel technology is effective in eliminating low adhesion problems due to contamination build-up.
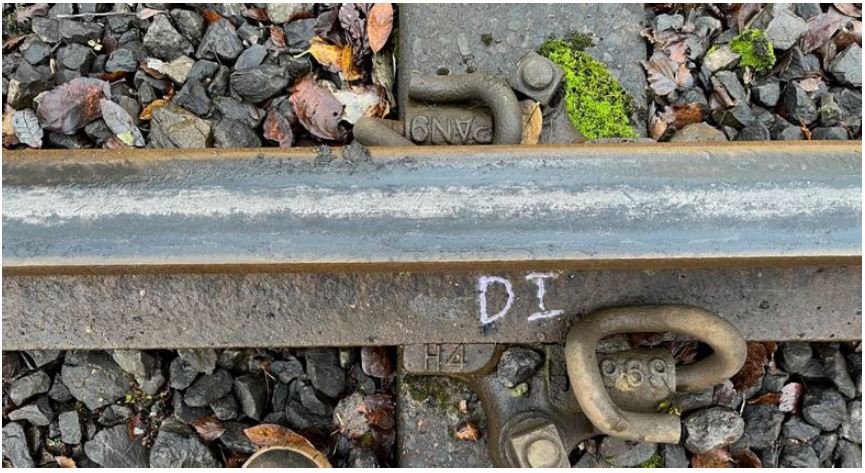
Conclusions
The railhead leaf layer, representative of autumn conditions, exhibited ultra-low friction coefficients. The innovative abrasive/water cleaning system resulted in a significant increase in friction, meeting operational braking requirements. Further research could compare friction coefficients before and after standard railhead treatment train cleaning to assess the novel technology’s performance against traditional methods. This case study highlights the effectiveness of the developed railhead cleaning technology and provides a foundation for future investigations into standardizing and improving railhead cleaning technologies.
Do you have any questions?
Our sales team will be happy to help. You can reach us by telephone from Monday to Friday between 8 am and 4 pm.