THE MOST EFFICIENT WAY OF WATERJET CUTTING
Technology
Continuous cutting process
What is ConSus® and what makes it so special?
What is the advantage of continuous cutting processes?
How does the continuous cutting process work?
Where is ConSus® suitable for use?
The system is primarily used stationary in the processing industry as well as in contract manufacturing. Whether special materials with enormous material thickness and special properties, ceramic and glass types, high-performance metal alloys or modern composite materials and plastics – ConSus® has almost no limits in separation.
Where can I get more information?
ConSus® explained shortly:
- 1. Generate pressure
Water is supplied with a high-pressure pump of up to 1500 bar. - 2. Suspension
A suspension is generated from water and abrasive sand in the high-pressure vessel. - 3. Level monitoring
Abrasive is refilled from the intermediate container into the high-pressure container at the same pressure ratio. - 4. Pressure is converted into speed
The suspension is forced through the nozzle and transformed into a cutting jet.
Continuous cutting process
You are currently viewing a placeholder content from YouTube. To access the actual content, click the button below. Please note that doing so will share data with third-party providers.
More InformationDo you have any questions?
Our sales team will be happy to help. You can reach us by telephone from Monday to Friday between 8 am and 3 pm.
Blog
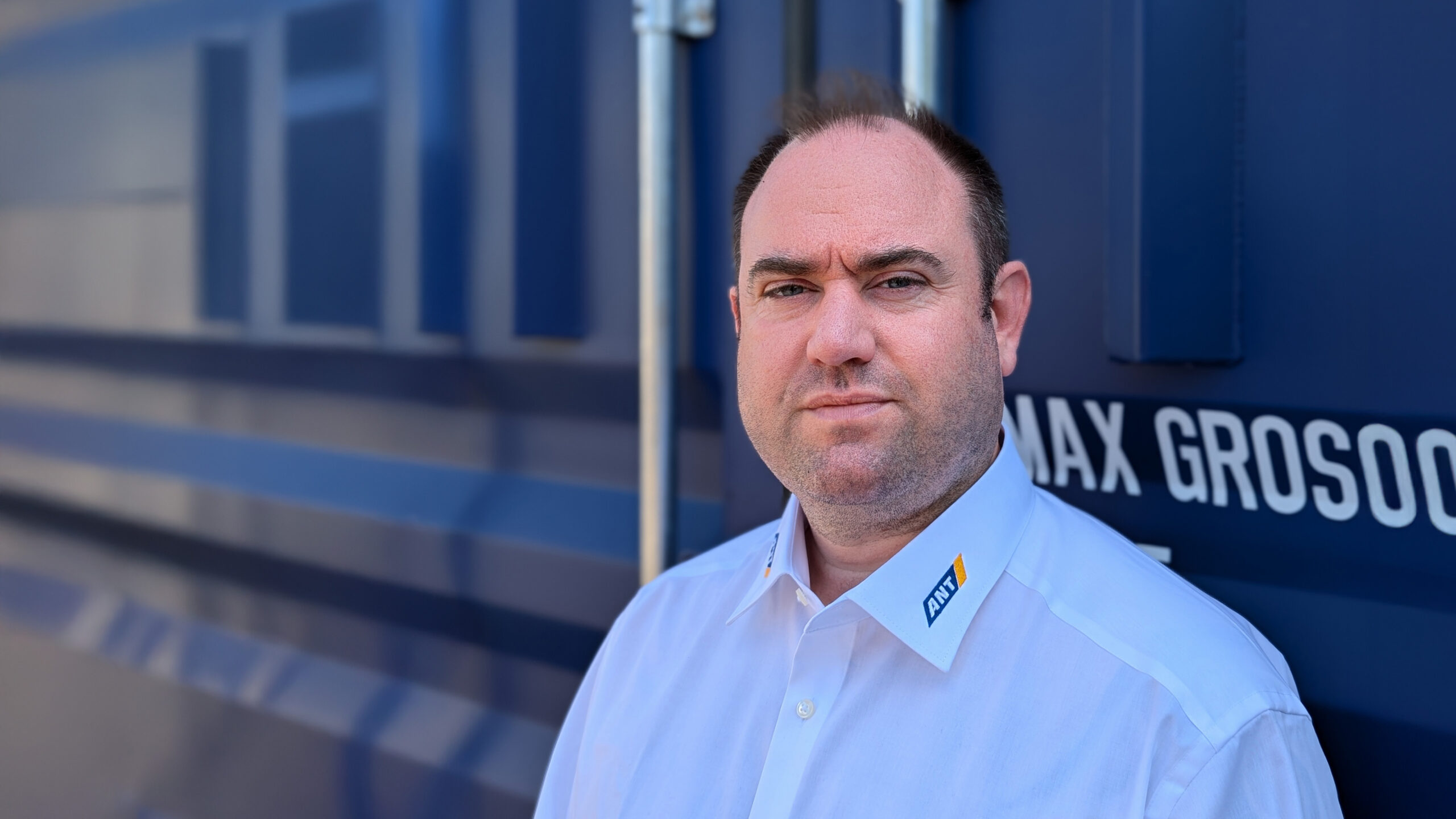
Sales Manager – Interview with Steve Allright
Inside Sales at ANT: Steve Allright on Customer Perspective, Industry Change, and Why He Sees ANT as a Technology Game-Changer
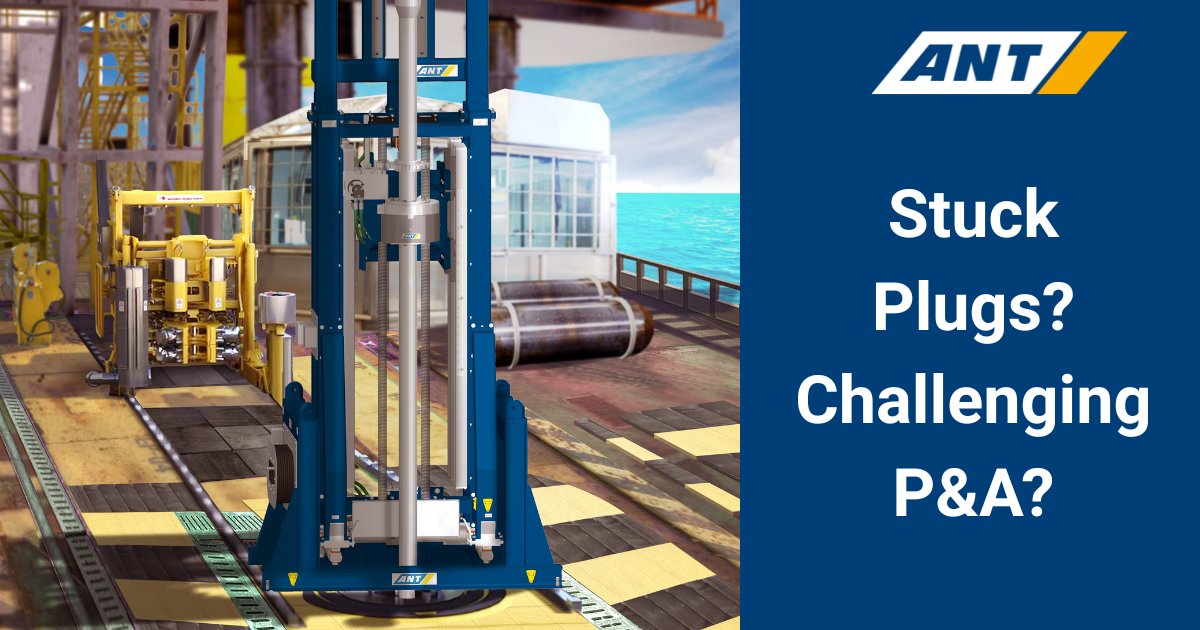
P&A: Testing the New Topside Drive System for Next-Gen Downhole Erosion
Discover wellANT – the modular, rig-less erosion tool for safe and efficient plug & abandonment.
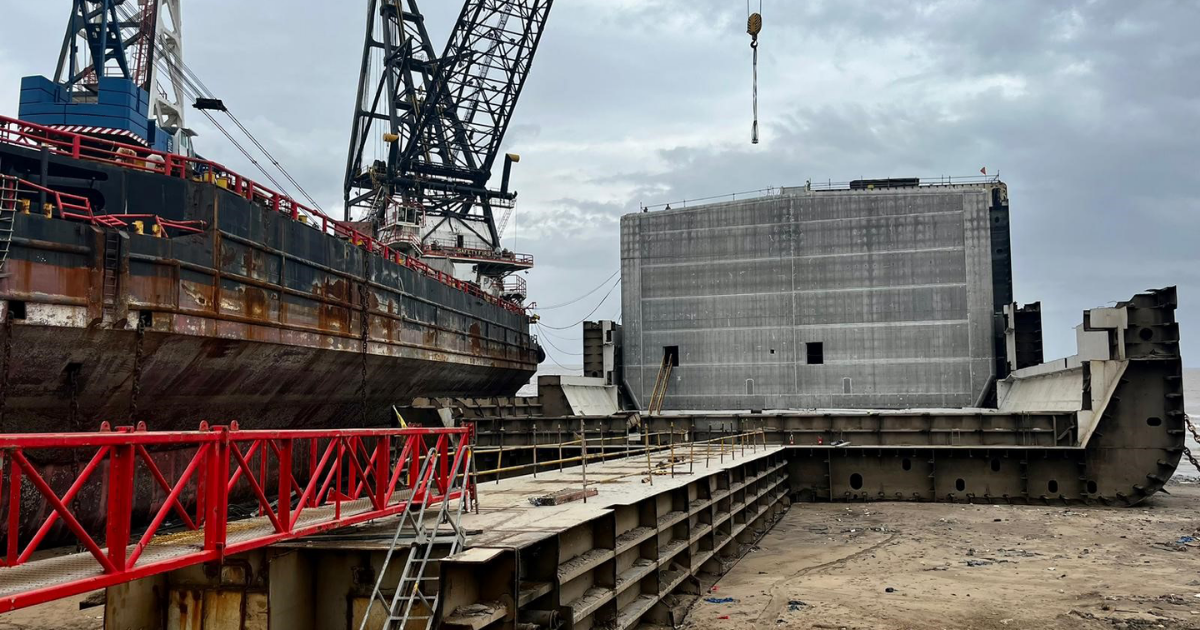
Scientifically Proven: Waterjet Technology as a Key Enabler for Safe and Sustainable Ship Recycling
A scientific study confirms: waterjet cutting significantly reduces emissions and risks in ship dismantling. Discover how mobile waterjet systems offer a safe, scalable, and sustainable alternative.