Waterjet cutting: safe, efficient and sustainable
WATERJET CUTTING: A CUTTING-edge TECHNOLOGY
Waterjet cutting - a cutting technology in detail
Waterjet cutting is a fascinating manufacturing process that may appear unusual at first glance: it utilizes high-pressure water jets to cut materials with precision. In this article, we will delve deep into this separation technique, explore its various variations, and highlight its advantages over other cutting technologies.
What is Waterjet Cutting?
Waterjet cutting is a manufacturing process in which a workpiece is separated using a high-pressure water jet (cutting method), thus categorizing it as a cold cutting technology. It can be classified into pure waterjet cutting and abrasive waterjet cutting. ANT AG has revolutionized abrasive waterjet cutting and is now a technology leader in the field of Water Abrasive Suspension (WAS).
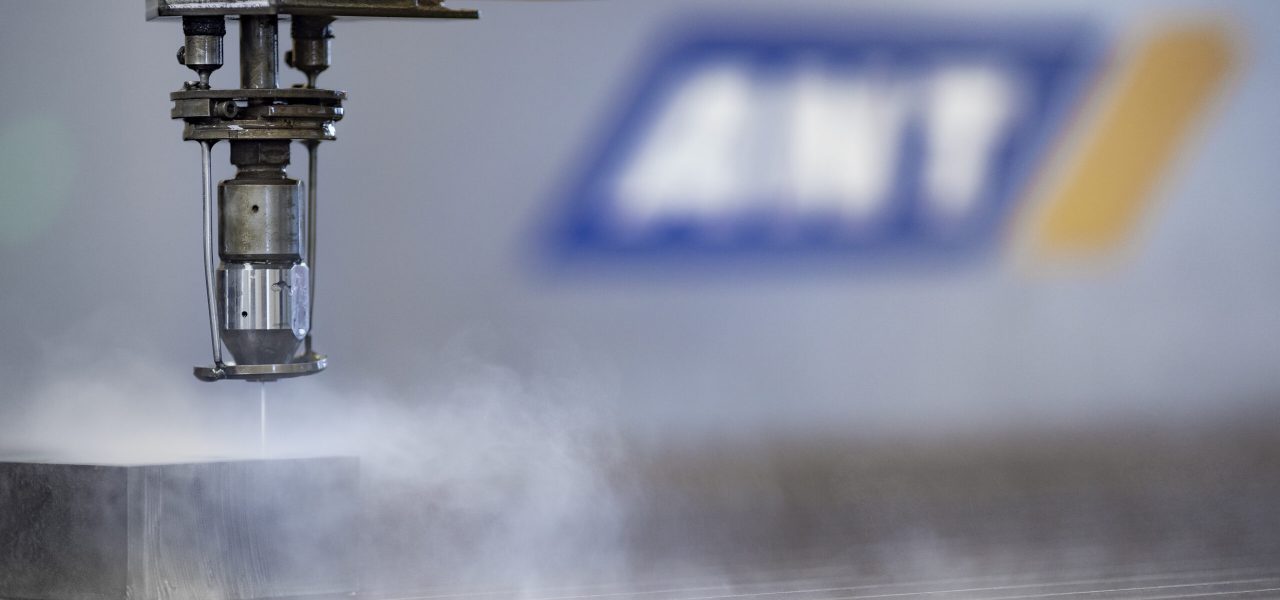
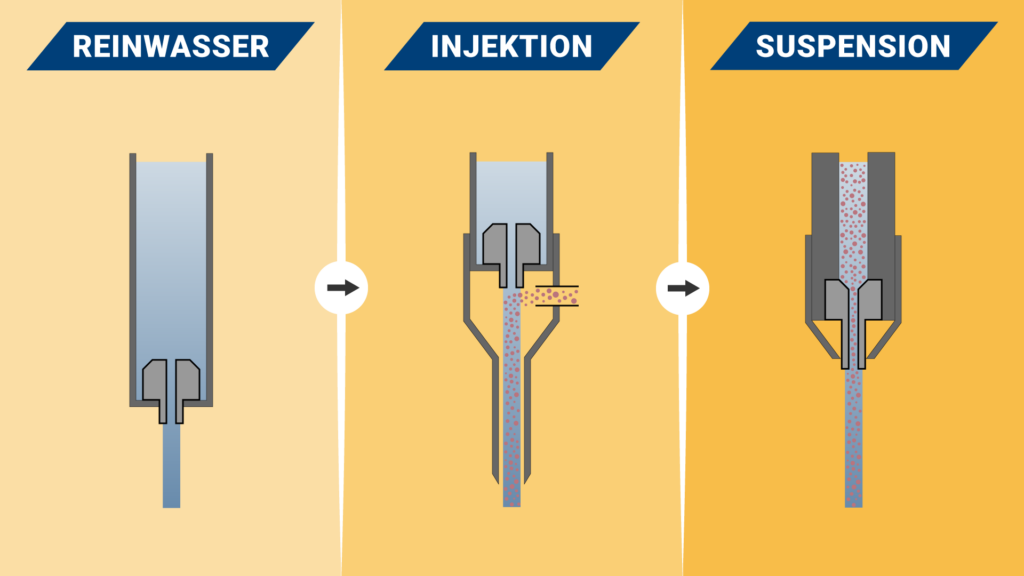
In pure waterjet cutting, only pure water is used to cut the material. This is particularly suitable for soft materials such as rubber, foam, and thin plastics where abrasive particles are not required.
In this variant, a cutting additive is introduced into the water jet to enhance cutting performance. This additive can include abrasive particles such as sand or garnet. Injection waterjet cutting is suitable for a broader range of materials, including metals, ceramics, and composite materials.
Suspension waterjet cutting is an advanced form of injection waterjet cutting. Here, a mixture of water and abrasive particles is created in a suspension tank before being injected into the cutting head. This allows for better control of the abrasion process and provides the flexibility to adjust the abrasive medium according to the requirements of the material being cut. Suspension waterjet cutting is often used for cutting thick and harder materials such as metals and composite materials.
Explanation of Waterjet Cutting (Pure Water, Injection, Suspension)
Waterjet cutting is classified as a cold cutting method and can be divided into various categories, including pure waterjet cutting and abrasive waterjet cutting, which is further distinguished into Water Abrasive Injection System (WAIS) and Water Abrasive Suspension System (WAS).
In pure waterjet cutting, only pure water is used, whereas in WAIS and WAS, abrasive materials like garnet sand are added to enhance cutting performance.
What is Abrasive Waterjet Cutting and where is it used?
Abrasive waterjet cutting can be divided into the Water Abrasive Injection System (WAIS) and the Water Abrasive Suspension System (WAS), which is patented by ANT. In both methods, an abrasive material such as garnet sand must be mixed with the water jet. WAS is primarily used for high-strength, thick, demanding, and tensile materials.
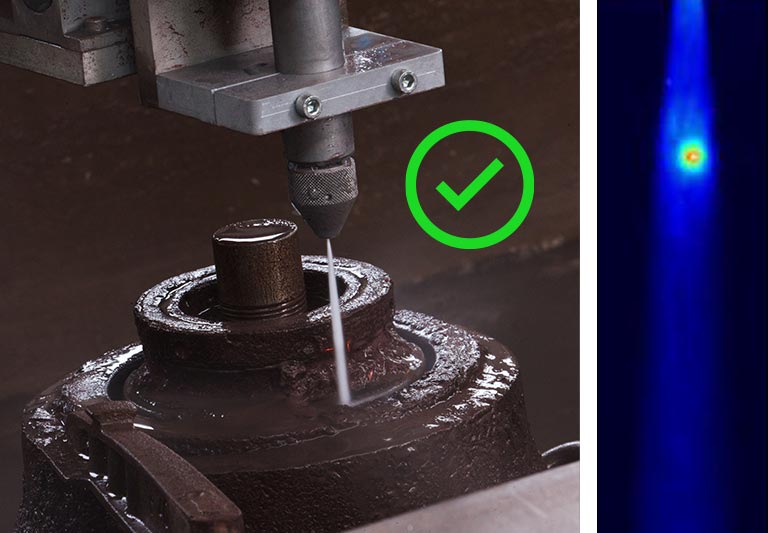
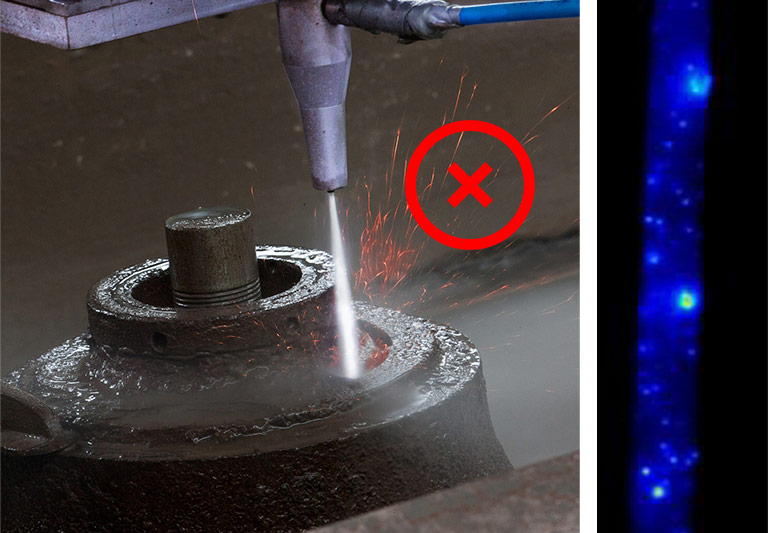
The ANT basic technology WAS explained shortly:
- 1. Generate pressure
Water is supplied with a high pressure pump of up to 2500 bar. - 2. Suspension
A suspension is generated from water and abrasive sand in the high-pressure vessel. - 3. Pressure is converted into speed
The suspension is forced through the nozzle and transformed into a cutting jet.
How do WAIS and WAS differ, and what advantages does the ANT technology offer?
In WAIS (Water Abrasive Injection System), water flows through the nozzle in the cutting head of the system at very high pressure. The abrasive material is drawn into the mixture chamber through a vacuum (Venturi principle). This results in a third phase consisting of approximately 95 percent air, leading to turbulent mixing losses and reducing the overall efficiency of the cutting jet by approximately one-third.
In ANT WAS (Water Abrasive Suspension System) systems, on the other hand, a portion of the pressurized water flows through a bypass valve into the mixing unit (AMU). There, water and abrasive material form a suspension. The water abrasive suspension is directed through a high-pressure hose to the cutting nozzle and pushed through it. The potential energy of the pressure is transformed into a cutting jet within the nozzle, which exits at nearly twice the speed of sound. The result is a two-phase jet consisting of approximately 97.5 percent water and 2.5 percent abrasive. Since the abrasive particles in WAS systems are directly bound within the water, the ANT suspension jet is significantly more stable, precise, and powerful than the injection jet, and it is free of air. Due to the unique ANT nozzle geometry, WAS systems operate without the need for extremely high pressure, saving resources.
In summary, the ANT WAS technology provides a more stable, precise, and powerful cutting performance compared to the traditional WAIS method while also conserving resources.

Waterjet Cutting vs. Plasma, Laser and CNC
Waterjet cutting has its unique advantages compared to other cutting technologies such as laser, plasma, and milling. In this section, we will take a closer look at these differences and demonstrate why the cutting technology of our choice can be the better option in many application areas.
When it comes to the cutting material, waterjet cutting knows no bounds. It is excellent for cutting a wide range of materials, including metals, plastics, ceramics, glass, stone, and composites. In contrast, laser and plasma cutting technologies have more limited material diversity and often require specific settings for each material. What sets the waterjet apart is its effectiveness across various materials, without any material limitations.
Waterjet cutting is suitable for a wide range of material thicknesses, from thin foils to thick metal plates. Laser and plasma cutting have limited cutting depths, which can pose restrictions when dealing with thicker materials. Water Abrasive Suspension (WAS) can cut through material thicknesses of up to 1,000 mm.
Waterjet cutting is safer for operators as it does not produce harmful fumes or radiation. Laser and plasma cutting processes require special safety measures to protect the health of operators. Furthermore, Water Abrasive Suspension (WAS) can be used not only in the open air but also underwater. This can be operated remotely from a safe distance depending on the application, with a range of up to 1,000 meters.
Waterjet cutting does not generate heat during the cutting process. This means that the material properties remain unchanged and are not damaged by heat. In contrast, laser and plasma cutting processes generate high temperatures, which can lead to deformations, cracks, or melting issues, especially with sensitive materials.
Waterjet cutting allows for high precision and fine cuts without compromising material integrity. This technique can cut complex shapes and intricate details, which can be more challenging with laser and plasma processes due to heat-related effects.
Waterjet cutting is environmentally friendly as it does not generate hazardous fumes, gases, or smoke. In contrast, laser and plasma cutting processes can produce harmful emissions and waste that may be environmentally hazardous.
In milling or other mechanical cutting technologies, significant tool wear occurs, leading to increased operating costs. Waterjet cutting does not require tool changes and is therefore not subject to this wear and tear.
In summary, waterjet cutting can be the superior choice in many applications due to its material versatility, precision, environmental friendliness, and safety, especially when dealing with sensitive or diverse materials. WAS also offers significant advantages for high-strength, thick materials. It provides an efficient and cost-effective solution for separating workpieces of various thicknesses and shapes.
Waterjet Cutting: Which Sand, Which Abrasive Material?
Choosing the Right Abrasive Material
The selection of the appropriate abrasive material is crucial for the success of waterjet cutting. We will explore the various options for abrasive materials and explain how choosing the right material can influence the cutting process.
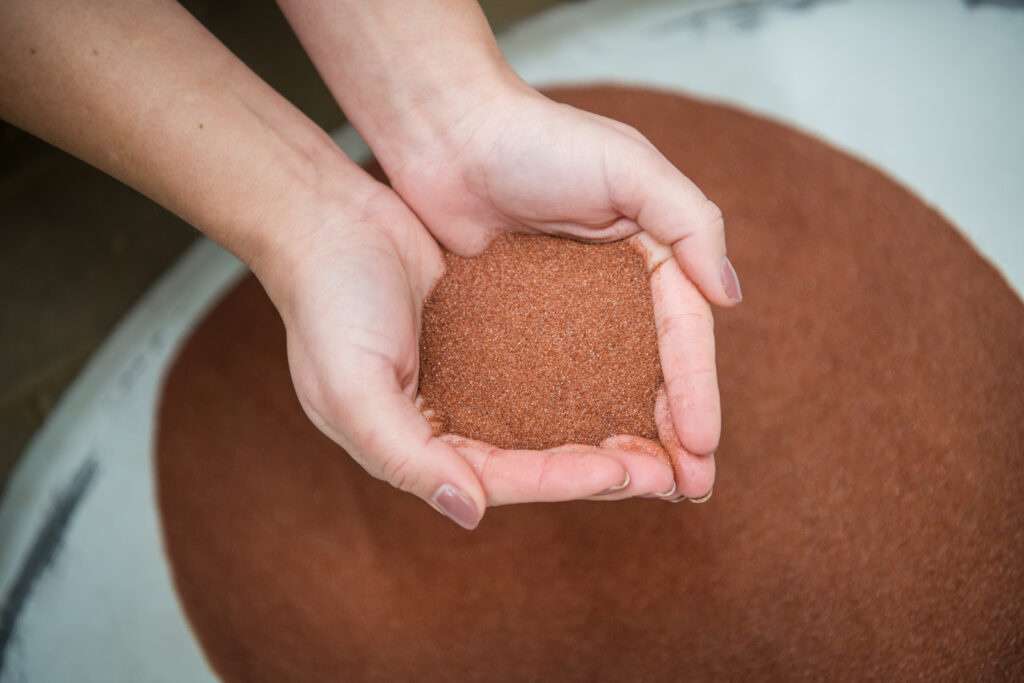
Garnet sand is a commonly used abrasive material for waterjet cutting. It is particularly effective in cutting hard materials such as steel, stainless steel, and stone. Garnet sand offers a good balance between cutting performance and wear resistance.
Frequently, mineral abrasives such as sand are used in waterjet cutting. This abrasive material is added to the water jet to enhance cutting performance. The particle size of the abrasive material can be adjusted based on the material being cut and the cutting requirements. It is well-suited for cutting metals, glass, ceramics, and composite materials.
This abrasive material is often used for cutting aluminum and other soft metals. It is less aggressive than garnet sand and can help minimize oxidation.
Silicon carbide is used for cutting materials like glass, ceramics, and composite materials. It offers good precision and clean cuts.
Waterjet cutting with pure water is best suited for soft materials like rubber, foam, paper, and some plastics. It produces clean cuts without abrasive particles and is environmentally friendly.
The choice of the right abrasive material depends on various factors, including the material to be cut, desired cut quality, cutting speed, and cost considerations. Careful selection of the abrasive material to match the specific requirements of the cutting process is crucial for achieving the best results.
WAS (Water Abrasive Suspension) - water jet can cut through anything
WAS (Water Abrasive Suspension) cutting is not limited in terms of the range of materials it can cut. The cutting process is contactless, with no heat generation or deformation. This special type of waterjet cutting is used both in the open air and underwater, as well as in explosive and sensitive environments. Depending on the application, WAS allows for safe remote cutting of material thicknesses up to 1,000 mm from distances of up to 1,000 meters.
You are currently viewing a placeholder content from YouTube. To access the actual content, click the button below. Please note that doing so will share data with third-party providers.
More InformationDo you have any questions?
Our sales team will be happy to help. You can reach us by telephone from Monday to Friday between 8 am and 3 pm.
Blog
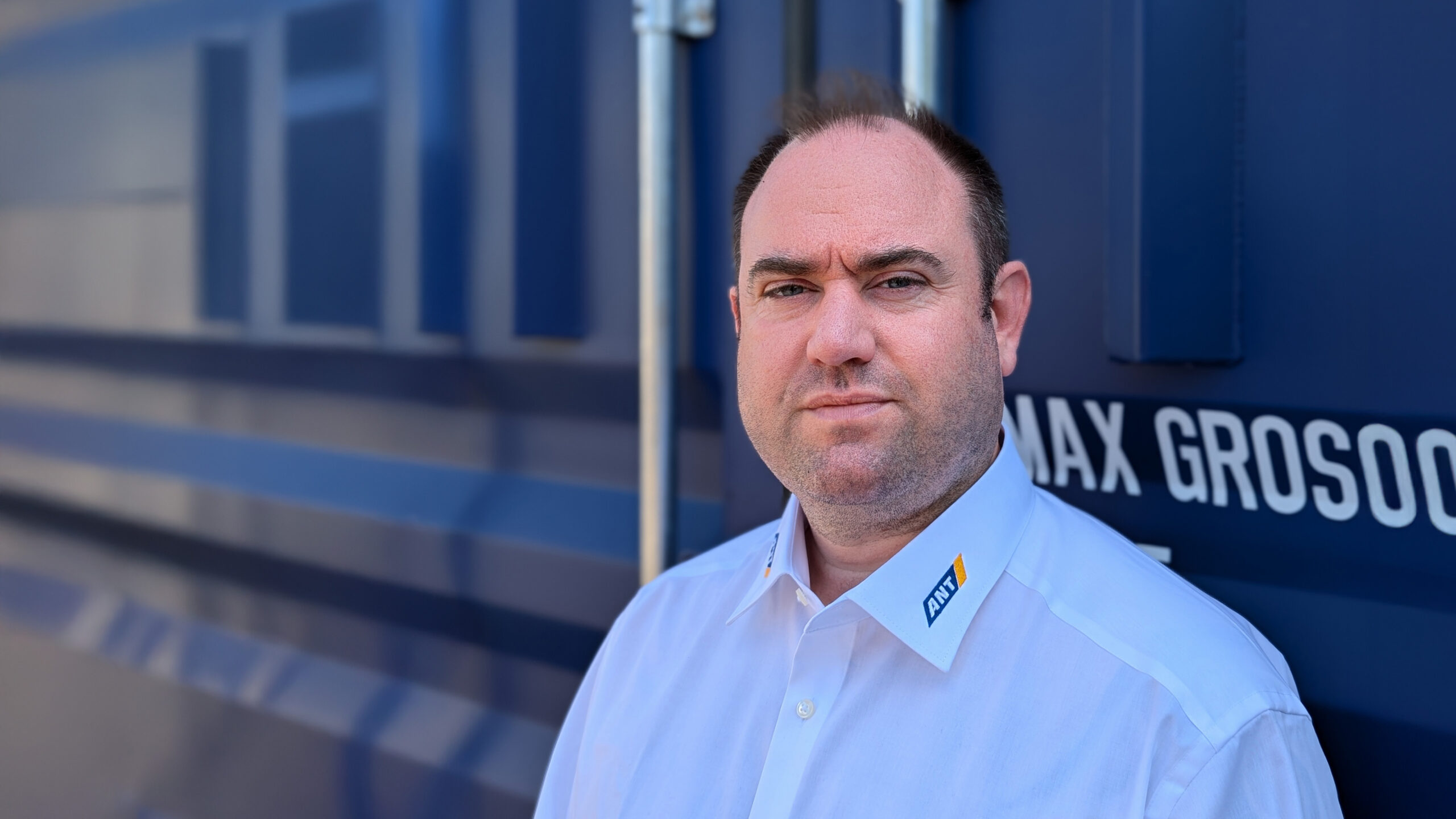
Sales Manager – Interview with Steve Allright
Inside Sales at ANT: Steve Allright on Customer Perspective, Industry Change, and Why He Sees ANT as a Technology Game-Changer
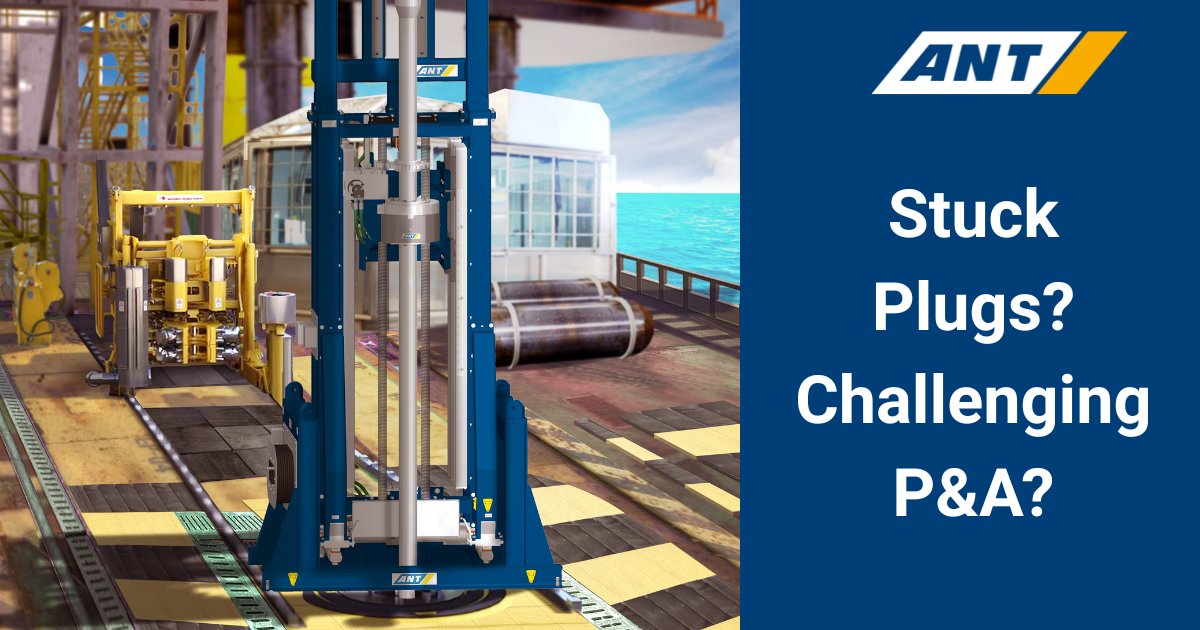
P&A: Testing the New Topside Drive System for Next-Gen Downhole Erosion
Discover wellANT – the modular, rig-less erosion tool for safe and efficient plug & abandonment.
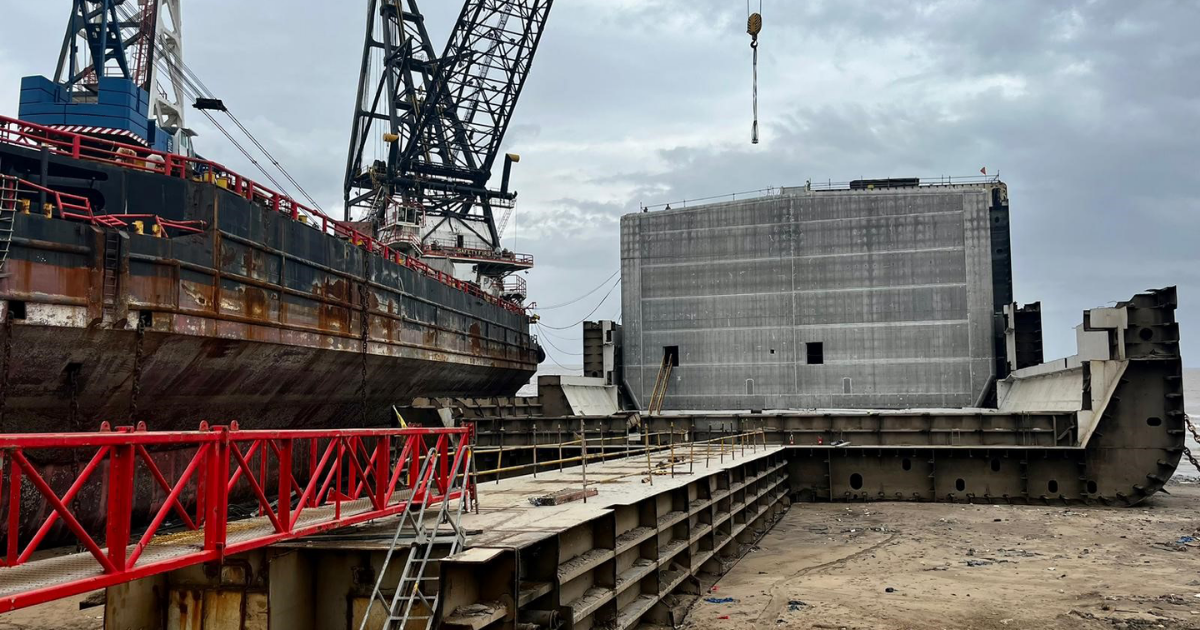
Scientifically Proven: Waterjet Technology as a Key Enabler for Safe and Sustainable Ship Recycling
A scientific study confirms: waterjet cutting significantly reduces emissions and risks in ship dismantling. Discover how mobile waterjet systems offer a safe, scalable, and sustainable alternative.