Friction measurements to assess the performance of a new water/abrasive railhead cleaning system
1. Introduction
Autumnal leaf fall causes leaves to be deposited directly on the railhead or be picked up and redeposited
by airflow caused by vehicle passage. This organic material reacts and bonds to the railhead
to form a black layer which causes ultra-low friction conditions.
A new abrasive/water jetting railhead cleaning system has been designed to remove this layer. This
system was trialled on-board a Class 153 vehicle at East Lancashire Railway. Four days of trials were
carried out, between 28/11/23 and 01/12/23.
A representative organic layer was formed by placing powdered leaf material on the railhead and
rolling with a vehicle until it had blackened and bonded to the underlying steel.
A Rivelin Rail portable railhead tribometer was used to measure friction before and after cleaning. This,
alongside railhead imaging and layer thickness data, was used to quantify cleaning performance.
2. Method
2.1 Location
Testing was conducted at East Lancashire Railway (ELR). Test site 1 was initially selected for testing, in
a cutting on the west side of a bridge. Testing was carried out here on 28/11/2023.
Due to cold weather freezing the rail and producing an ice layer in the mornings, the site was moved
into direct sunlight further from the bridge (Site 2) for the remainder of the trial (days two-four,
29/11/2023-01/12/2023).
On each test site: a 10 m section was marked out and six measurement locations labelled with acrylic
pen, three on each rail over the 10 m distance. The map of the test sites and a schematic of
measurement locations are shown in Figure 1.s
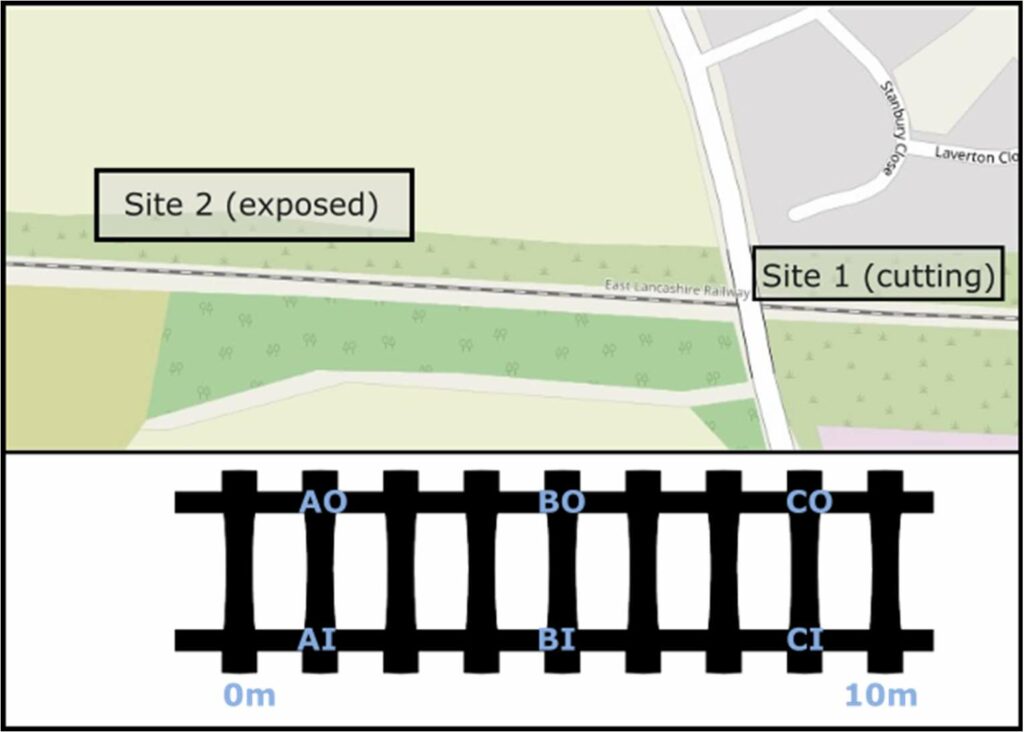
Figure 1 A map of the test sites and schematic of the measurement locations
2.2 Railhead conditioning
Conditioning was carried out to create a representative level of leaf contamination that would produce
low friction conditions and require cleaning during the autumn season. A suitable leaf layer formation
method was used, this method has previously been developed by The University of Sheffield and is
briefly described below.
The rail was oxidised, typical of an irregularly used heritage railway. To remove the oxide layer, the
railhead was lightly sanded with a sanding star drill attachment. This exposed the bare steel, allowing
quicker reaction with leaf material. Blended fresh Sycamore leaves were then placed on the railhead
by hand.
A Pacer, provided by ELR (Figure 3), was rolled over the leaf layer at approximately 10 mph between
two and eight times. This blackened the leaf layer and caused it to bond with the steel. This process is
show in Figure 2.

Figure 2 Flow chart of leaf layer formation process
On day one (28/11/2023) the railhead and vehicle wheels were wet due to damp morning conditions
before leaf layer application. The leaf layer addition and roll over with the Pacer were repeated three
times because the leaf material was being picked up and removed by wet wheel passage.
For days two-four (29/11/2023-01/12/2023) conditions remained consistent, with cold but dry
weather. The leaf layer quickly bonded with the railhead so a single leaf layer application could be
carried out.
Example images before leaf powder application after leaf powder application (step 3) and then the
blackened leaf layer after vehicle rollover are shown in Figure 3.
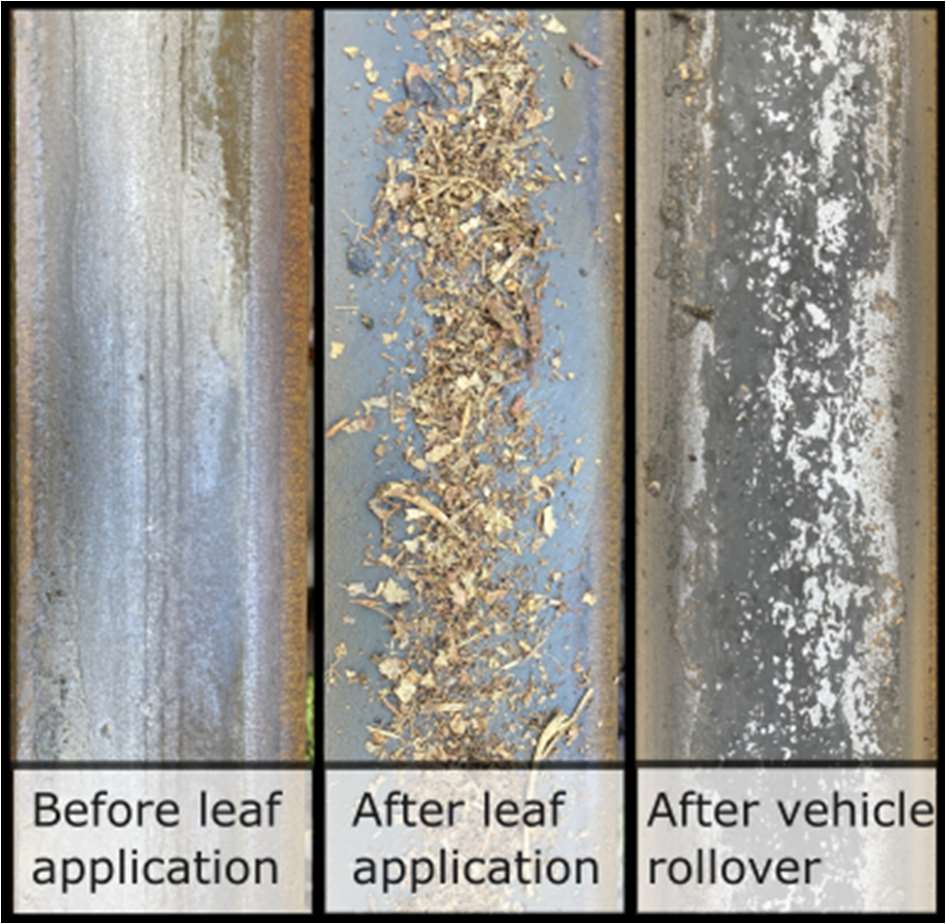
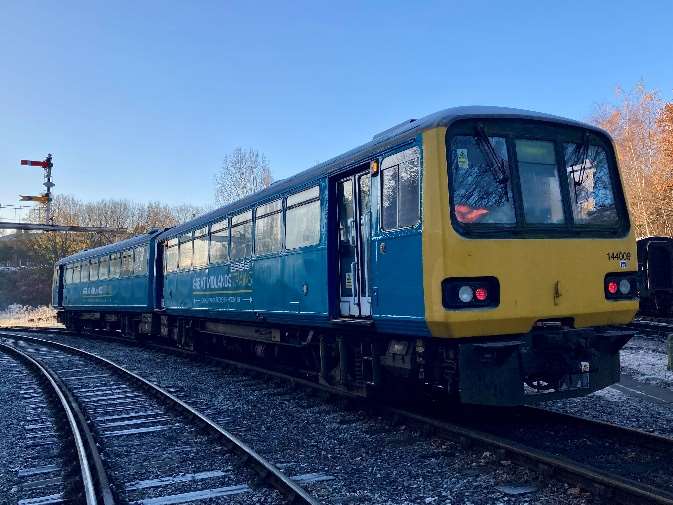
Figure 3 Railhead images during the leaf conditioning, showing the blackening on the leaf material after vehicle passage (L);
the Pacer used for leaf layer conditioning (R)
2.3 Railhead measurements
The Rivelin Rail portable railhead tribometer was used to measure railhead friction. This magnetically
clamps to the railhead and uses a freely rotating ER8 steel wheel as the counter body to the rail. The
wheel rolls along a 300 mm length of rail at 200 mms-1. The wheel’s axis of rotation is rotated to an
angle with the direction of travel which produces lateral creep in the contact. The resultant force on
the ball is measured with a sampling frequency of 100Hz. The lateral creep can be converted to an
effective linear creep by taking the tangent of the angle, throughout this report this conversion has
been applied. An image of the tribometer is shown in Figure 4. For this work, tests were carried out at
700 MPa contact pressure and 3% effective linear creep (30mrad angle).
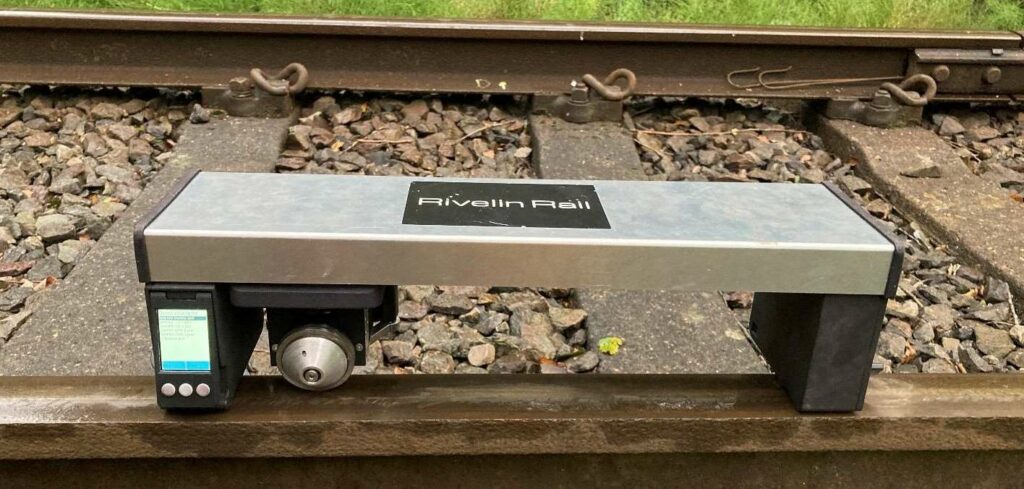
Figure 4 The Rivelin Rail portable tribometer
Friction measurements were taken as indicated in Figure 2 and after each cleaning run. Friction
coefficient was measured when the rail was wet. This was deemed the most appropriate technique to
assess how much leaf material was remaining, as leaf layers may not produce low friction and impede
braking when dry. Due to melting frost the railhead was also wet in places and the cleaning system
applied water, which made dry baseline values impossible to measure at times.
An eddy current layer thickness measuring device was used to measure layer thickness to Network Rail
procedure (Eddy Current Training Brief, Network Rail, 2010). At least 5 measurements were taken per
measurement location.
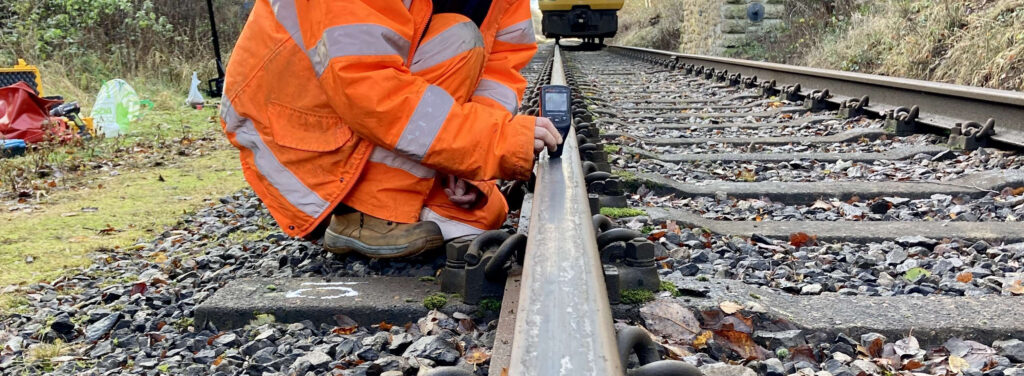

Figure 5 The eddy current thickness measuring device (upper) and designated contaminaon levels (lower) for leaf layer thickness, determined by Network Rail (Eddy Current Training Brief, Network Rail, 2010)
2.4 Railhead cleaning
A Class 153, equipped with the novel railhead cleaning system was stored at the Bury Street station
until test runs were required. When the leaf layer was prepared, this cleaning vehicle was driven in the
easterly direction over the test site at a designated speed, shown in Table 1. On two days (28/11/23
and 02/11/23) a second cleaning run was carried out. The cleaning system was run at 750 bar, using
1kg/minute of abrasive particles and 11 litre/min water.
2.5 Summary
The method for a typical test run can be summarised as:
1) Sand rail surface
2) Spray with water and measure wet baseline friction coefficient at six marked locations
3) Lay leaf powder by hand
4) Roll over leaf layer with Pacer
5) Repeat steps 3 and 4 until a black layer has been formed
6) Spray marked locations with water and measure wet leaf contaminated friction coefficient
7) Cleaning run with Class 153
8) Spray marked locations with water and measure wet cleaned friction coefficient
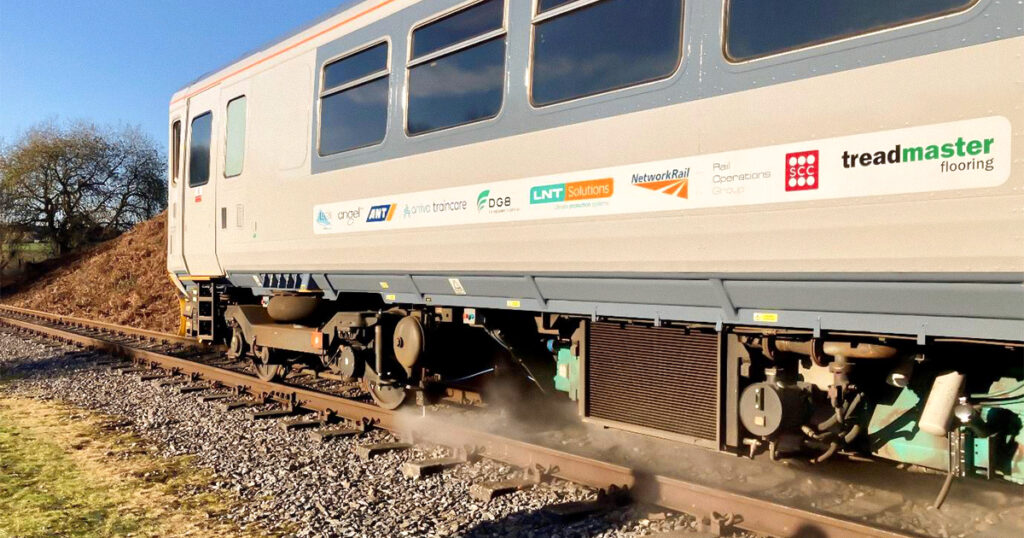
Figure 6 The Class 153 cleaning train, with the abrasive/water system spraying behind the second axle
Speed (mph) | ||
Date | Cleaning run 1 | Cleaning run 2 |
28.11.23 | 60 mph | 25 mph |
29.11.23 | 60 mph | – |
30.11.23 | 40 mph | – |
01.12.23 | 30 mph | 30 mph |
Table 1 Cleaning run speeds
3. Results
A boxplot summary of friction measurements for each day of testing are shown in Figure 7. A Kernel
Density Estimation plot, showing the distribution of data is shown in Figure 8.
Wet baseline friction measurements for Site 1 (0.16) were lower than the mean average for Site 2
(0.24). Site 1 was in a shaded cuttng with nearby trees so likely had some pre-existing organic
contamination. It had also been used as a test site in September forming leaf layers, so this may have
contributed.
The mean average friction coefficient for wetted leaf layers was 0.042, which would be classed as ultralow
adhesion. The driver of the Pacer stated that he had to take care with traction and braking because
he could feel the wheels slipping and sliding.
As shown in Table 2, on all four test days there was a statistically significant increase in friction after
the first cleaning pass (t-test against leaf layer values, n=6). The mean average friction coefficient after
one cleaning pass was above 0.09 on all test days, the minimum value required for braking under
typical GB timetabled operation (A Survey of Wheel/Rail Friction, E. Magel, 2017). When a second
cleaning pass was carried out, it increased the friction coefficient further.
Environmental conditions for each of the test days are shown in Table 3. Sample railhead images from
measurement site AO for each of the test days are shown in Figure 9. Visible railhead cleaning took
place for each of the test runs, but some visible leaf layer still remained in the running band.
A boxplot for layer thickness for each rail condition, measured using the Eddy current device, is shown
in Figure 10. Layer thickness measurements average as “medium” contamination level (15-30 μm)
through Network Rail guidelines (Eddy Current Training Brief, Network Rail, 2010). Thickness
measurements were not carried out on 29/11/2023. There was a decrease in average layer thickness
measurements between the “leaf layer” conditions and those after the first cleaning pass over all
measurement days.
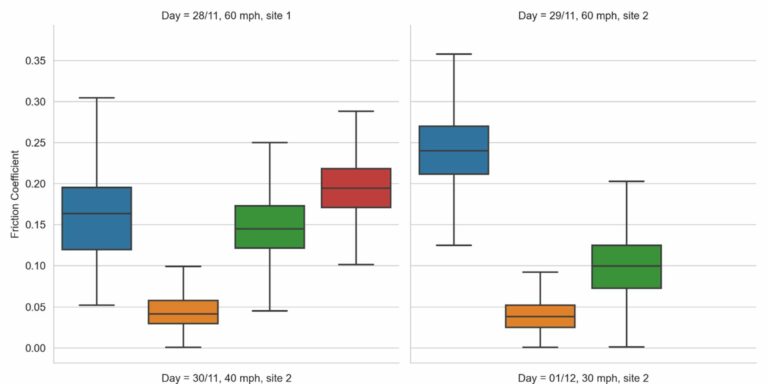
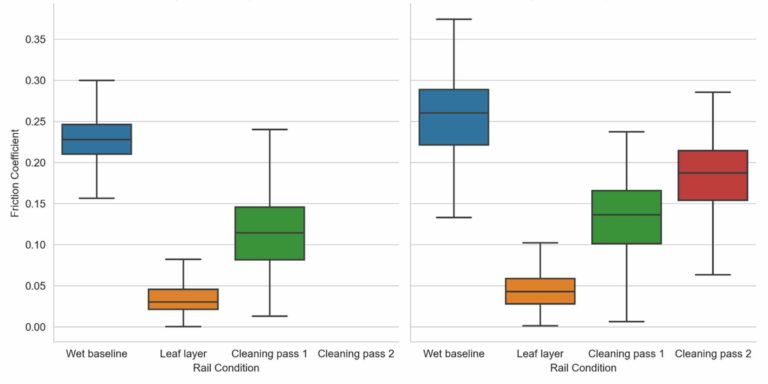
Figure 7 A boxplot of railhead conditions, over the four days of testing. The central line indicates the median, the box the 25th and 75th percentiles and the “whiskers” the minimum and maximum values
Mean average friction coefficient measurement
Day | Wet baseline | Leaf layer | Cleaning pass 1 |
28.11.2023 | 0.16±0.047 | 0.045±0.022 | 0.14±0.041 (p<0.00001) |
29.11.2023 | 0.24±0.048 | 0.039±0.018 | 0.10±0.039 (p<0.0001) |
30.11.2023 | 0.23±0.030 | 0.035±0.018 | 0.11±0.043 (p<0.00001) |
01.12.2023 | 0.26±0.045 | 0.045±0.021 | 0.13±0.044 (p<0.0001) |
Table 2 Mean average friction coefficients for each railhead condition tested using the Rivelin Rail tribometer, on Site 1 and Site 2
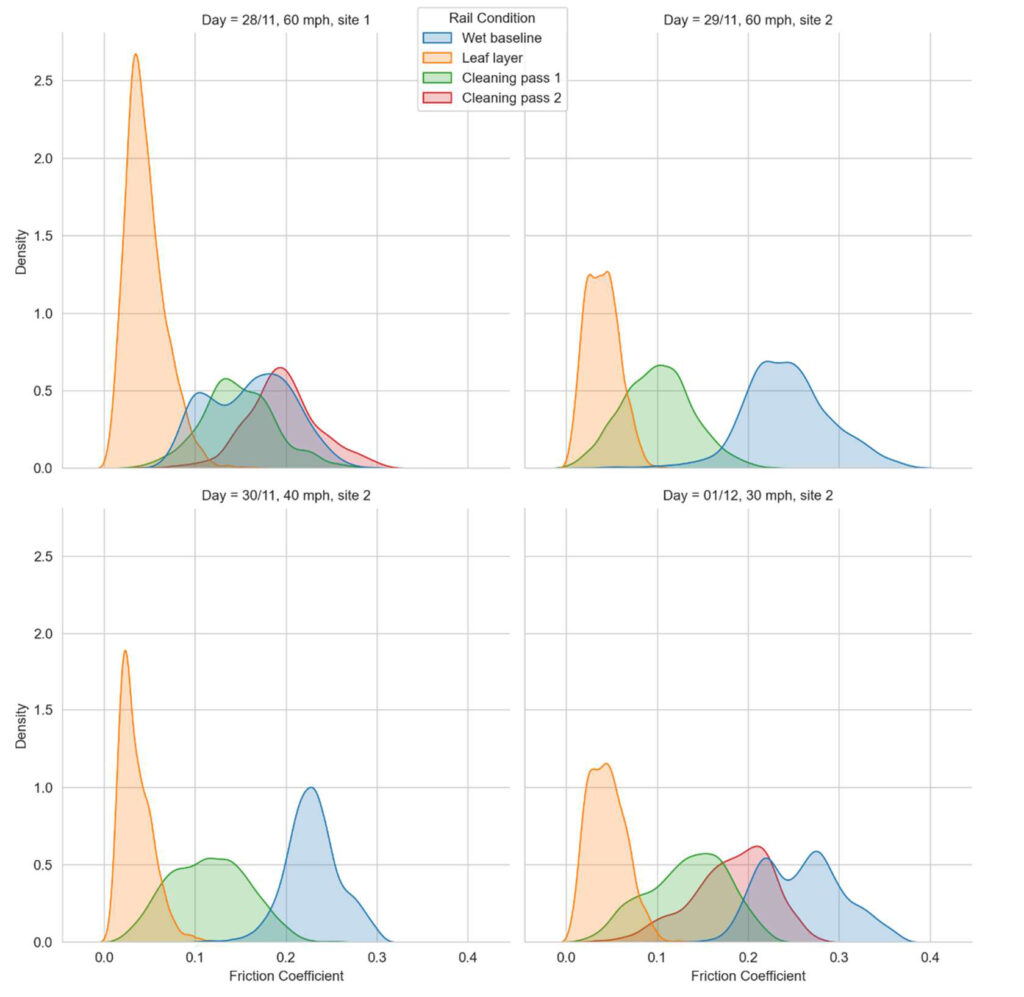
Figure 8 A kernel density estimation plot of rail conditions over the four days of testing, showing the distribution of friction coefficient measurements
Day | Railhead temperature in °C | Air temperature in °C | Relative humidity (%) | Weather conditions |
28.11.2023 | 1,8 | 2,6 | 95 | Overcast |
29.11.2023 | 5,9 | 8,4 | 84 | Sunny |
30.11.2023 | 4,2 | 6,8 | 81 | Sunny |
01.12.2023 | 4,6 | 9,5 | 56 | Sunny |
Table 3 Environmental data for each day of testing
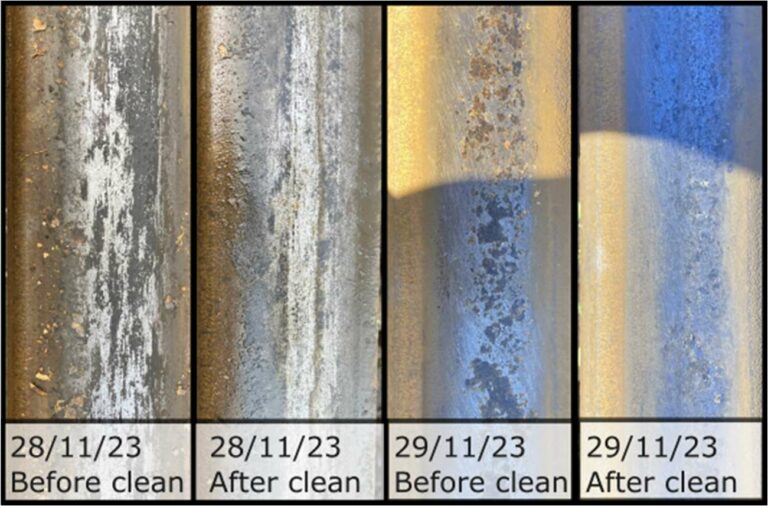

Figure 9 Sample railhead images from site AO, for each of the cleaning test runs
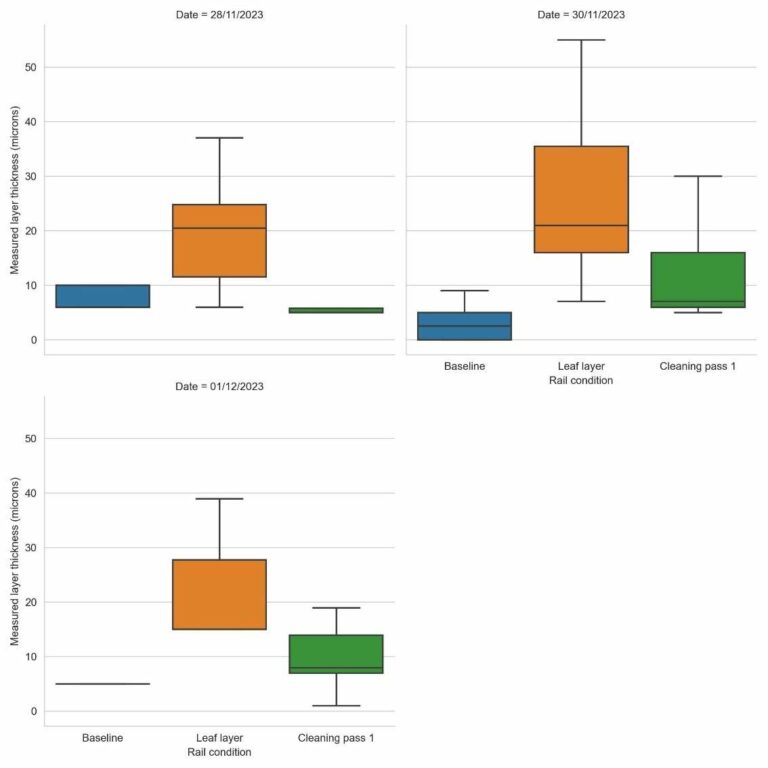
Figure 10 Layer thickness, measured using an eddy current device, for each rail condition for three days of testing (layer thickness not measured on 29/11/2023)
4. Conclusions
A railhead leaf layer was formed to represent typical autumn conditions. This was visibly blackened
and bonded to the rail steel due to vehicle passage. When friction was measured using the Rivelin Rail
portable tribometer this layer produced an ultra-low friction coefficient (mean average 0.042) and
would have been classed as “medium” thickness according to Network Rail guidelines, the driver also
reported difficulties with traction and braking due to low adhesion issues.
After one cleaning pass using the novel abrasive/water cleaning equipment on-board a Class 153, there
was a statistically significant increase in friction coefficient. The mean average friction coefficient after
one cleaning pass was above 0.09 on all test days, the minimum value required for braking under
typical GB timetabled operation (A Survey of Wheel/Rail Friction, E. Magel, 2017).
The leaf layer was visibly cleaner, but leaf material remained in the rail running band and this did not
increase to wet baseline values. When a second cleaning run was carried out, there was an additional
increase in friction coefficient, on 28/11/2023 this increased to above the wet baseline value.
Future work could be carried out to obtain friction coefficient measurements before and after standard
railhead treatment train cleaning, to baseline cleaning performance as a comparison to novel
technologies.
Source: LNT